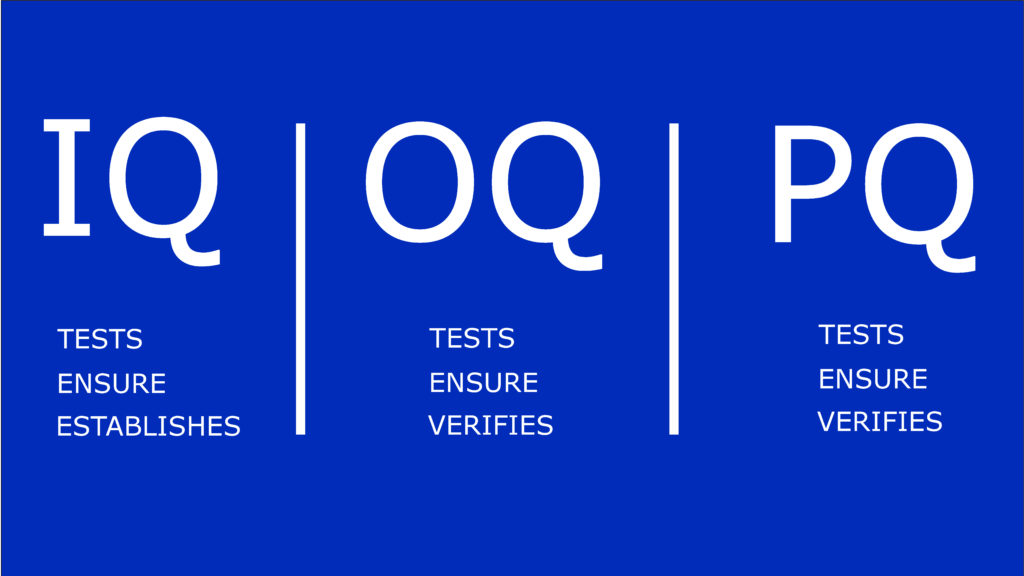
Interviewer: Can you explain what IQ, OQ, and PQ are and how they relate to warehouse and logistics auditing?
Brij: IQ, OQ, and PQ stand for Installation Qualification, Operational Qualification, and Performance Qualification, respectively. These are essential components of the validation process that help ensure the quality and consistency of products and services in the warehouse and logistics industry.
Installation Qualification (IQ) involves verifying that all the necessary equipment, hardware, software, and documentation are correctly installed and configured. This step ensures that the warehouse or logistics facility is equipped with everything it needs to operate correctly.
Operational Qualification (OQ) involves verifying that the equipment and processes are functioning correctly according to their specifications. This step ensures that all systems and processes are working as intended.
Performance Qualification (PQ) involves verifying that the equipment and processes are capable of consistently producing products or services of the required quality. This step ensures that all systems and processes are producing the desired output.
In the context of warehouse and logistics auditing, IQ, OQ, and PQ are important for ensuring that the warehouse or logistics facility is operating according to best practices and regulatory standards.
Interviewer: Can you explain how these audits are performed in practice?
Brij: Sure! In practice, IQ, OQ, and PQ audits involve a series of tests and documentation reviews that assess the facility’s compliance with industry standards and regulations.
For example, during an IQ audit, an auditor might review the facility’s equipment specifications, vendor qualifications, and installation documentation. They might also perform physical inspections of the facility’s equipment to ensure that everything is installed correctly.
During an OQ audit, an auditor might perform functional tests on the facility’s equipment to ensure that it is functioning correctly according to its specifications. This might involve running simulations or performing real-world tests to verify that the equipment is operating as intended.
Finally, during a PQ audit, an auditor might perform statistical analysis on the facility’s products or services to ensure that they are consistently meeting quality standards. This might involve collecting data over a period of time and analyzing it to identify any areas of inconsistency or improvement.
Interviewer: What are some of the risks of not performing IQ, OQ, and PQ audits?
Brij: The risks of not performing IQ, OQ, and PQ audits are significant. Without these audits, there is no way to verify that the warehouse or logistics facility is operating according to industry best practices and regulatory standards. This can lead to inconsistent product or service quality, regulatory non-compliance, and even safety hazards.
For example, if a warehouse is not properly audited and documented, there may be safety hazards that could put employees at risk. Similarly, if a logistics facility is not properly audited and documented, there may be quality issues that could lead to product recalls or customer dissatisfaction.
Interviewer: Why is it important to have a good service provider for warehouse and logistics auditing?
Brij: It is essential to have a good service provider for warehouse and logistics auditing because auditing is a complex and specialized process that requires expertise and experience. A good service provider will have the knowledge, skills, and tools necessary to perform the audits effectively and efficiently. They will also be able to provide guidance and support to the facility in making any necessary improvements or adjustments.
Interviewer: How is the market for warehouse and logistics auditing changing?
Brij: The market for warehouse and logistics auditing is rapidly evolving as the industry becomes more complex and regulated. There is a growing demand for auditing services as companies strive to improve their operations and meet regulatory requirements.
Additionally, new technologies and innovations are emerging leveraging data,IoT and AI/ML. Exciting times indeed.
Ca you give us more details on IQ,OQ and PQ please?
IQ, OQ, and PQ are commonly known as Installation Qualification (IQ), Operational Qualification (OQ), and Performance Qualification (PQ). These are three important stages of a validation process used in the pharmaceutical, biotechnology, medical device, and other regulated industries to ensure that equipment, systems, and processes meet the required standards for quality and compliance with regulatory requirements.
The Installation Qualification (IQ) is the first stage of the validation process. It is a documented verification process that ensures that the equipment or system has been installed and configured correctly according to its specifications and manufacturer’s recommendations. This includes verifying that the equipment or system is installed in the correct location, that it is connected to the appropriate utilities, that it is properly calibrated and that all required components are in place.
The Operational Qualification (OQ) is the second stage of the validation process. It is a documented verification process that ensures that the equipment or system is operating within its specified limits and performance parameters. This includes testing the equipment or system under normal operating conditions and verifying that it is capable of producing accurate and reliable results.
The Performance Qualification (PQ) is the final stage of the validation process. It is a documented verification process that ensures that the equipment or system consistently produces accurate and reliable results over time. This includes testing the equipment or system under a range of operating conditions and verifying that it meets the required performance specifications.
In summary, IQ, OQ, and PQ are three stages of a validation process used to ensure that equipment, systems, and processes meet the required standards for quality and compliance with regulatory requirements. Each stage of the process has its own set of documented procedures and protocols to ensure that the equipment or system is installed, tested, and validated in a thorough and consistent manner.
How are the various steps in the above response practically done?
We have done many of these and for us it’s about a programmatic approach to solving the problem.
The various steps in IQ, OQ, and PQ are practically done through a systematic and documented validation process. The validation process typically involves the following steps:
- Define the validation protocol: The first step is to define a validation protocol that outlines the testing procedures and acceptance criteria for each stage of the validation process. This protocol should be based on regulatory requirements and industry best practices.
- Execute the IQ: The installation qualification (IQ) involves verifying that the equipment or system has been installed and configured correctly. This includes checking that the equipment or system is installed in the correct location, that it is connected to the appropriate utilities, that it is properly calibrated, and that all required components are in place. The IQ typically involves a combination of visual inspections, documentation reviews, and physical testing.
- Execute the OQ: The operational qualification (OQ) involves testing the equipment or system under normal operating conditions and verifying that it is capable of producing accurate and reliable results. This includes testing the equipment or system under a range of operating conditions, such as varying loads, speeds, and temperatures, and verifying that it meets the required performance specifications. The OQ typically involves a combination of physical testing, data analysis, and documentation reviews.
- Execute the PQ: The performance qualification (PQ) involves testing the equipment or system under a range of operating conditions and verifying that it consistently produces accurate and reliable results over time. This includes testing the equipment or system under realistic operating conditions, such as varying loads, speeds, and temperatures, and verifying that it meets the required performance specifications. The PQ typically involves a combination of physical testing, data analysis, and documentation reviews.
- Document the results: Throughout the validation process, all testing procedures, data, and results must be thoroughly documented. This documentation should be detailed, accurate, and complete, and should provide a clear record of the validation process and its outcomes.
- Review and approve: Once the validation process is complete, the results should be reviewed and approved by the appropriate stakeholders, including quality assurance personnel, regulatory agencies, and management.
In summary, the various steps in IQ, OQ, and PQ are practically done through a systematic and documented validation process that involves testing the equipment or system under a range of operating conditions and verifying that it meets the required performance specifications. Throughout the process, all testing procedures, data, and results must be thoroughly documented, and the results must be reviewed and approved by the appropriate stakeholders.
How do you ensure reliability of the results?
To ensure reliability of the results, it is important to follow a systematic and well-documented approach to validation. This includes using validated test methods and procedures, ensuring that the equipment or system is properly calibrated and maintained, and carefully documenting all testing procedures and results.
It is also important to establish appropriate acceptance criteria for each stage of the validation process, and to use statistical analysis to determine the reliability of the results. This may involve using statistical process control (SPC) techniques to monitor the performance of the equipment or system over time, and to detect any trends or deviations from the expected performance.
In addition, it is important to involve the appropriate stakeholders in the validation process, including quality assurance personnel, regulatory agencies, and management. This can help to ensure that the validation process is conducted in accordance with regulatory requirements and industry best practices, and that the results are reliable and meaningful.
Overall, ensuring reliability of the results requires a careful and well-planned approach to validation, along with appropriate documentation, statistical analysis, and stakeholder involvement.
Please tell us more about the statistical analysis in details?
I can’t stress how important this is for us when performing IQ,OQ and PQ for our clients. Statistical analysis is a key component of ensuring the reliability of validation results. It involves using mathematical and statistical techniques to analyze data and determine whether the results of a validation study are reliable and meaningful.
There are a number of statistical techniques that can be used in validation, including:
- Descriptive statistics: These are used to summarize and describe the data collected during the validation process. This can include measures of central tendency (such as mean or median) and measures of variability (such as standard deviation or range).
- Hypothesis testing: This is used to determine whether the results of a validation study are statistically significant. Hypothesis testing involves setting up a null hypothesis (which states that there is no significant difference between two groups or conditions) and an alternative hypothesis (which states that there is a significant difference). Statistical tests are then used to determine the probability of observing the data if the null hypothesis is true, and to reject or accept the null hypothesis based on this probability.
- Regression analysis: This is used to examine the relationship between two or more variables. Regression analysis can be used to determine whether there is a significant correlation between variables, and to develop predictive models based on this relationship.
- Statistical process control (SPC): This is used to monitor the performance of a system or process over time, and to detect any trends or deviations from expected performance. SPC involves using statistical techniques to analyze process data and determine whether the system is operating within acceptable limits.
Overall, statistical analysis is an important tool in ensuring the reliability of validation results. It allows us to assess the significance of our findings, identify trends and patterns in our data, and develop predictive models based on this information. By using appropriate statistical techniques and methods, we can ensure that our validation studies are rigorous, reliable, and meaningful.
What should folks watch out for from service providers ?
When choosing a service provider for warehouse and logistics auditing, there are a few things to watch out for to ensure that you receive high quality and reliable services:
- Qualifications and experience: It is important to choose a service provider who has the appropriate qualifications, expertise, and experience in conducting warehouse and logistics audits. Look for service providers who have relevant certifications, such as those from regulatory bodies or professional organizations, and who have experience working in your industry.
- Reputation: Look for service providers who have a good reputation in the industry. This can include checking online reviews, asking for references from previous clients, and reviewing the service provider’s track record of success.
- Services offered: Make sure that the service provider offers the specific types of audits and assessments that you need. This may include warehouse audits, transportation audits, cold chain assessments, and more.
- Compliance with regulations: Ensure that the service provider is familiar with and compliant with all relevant regulatory requirements and standards, including those related to food safety, quality control, and environmental regulations.
- Communication and transparency: Choose a service provider who communicates clearly and transparently throughout the audit process. This includes providing detailed reports and feedback, answering questions and concerns, and addressing any issues or challenges that arise.
-
Our qualified team of professionals would love to talk to you about questions or any requirements. Talk to our team now using the contact button for questions or needs.
Contact Us Via WhatsApp Contact Us Via Email Call Us Via Phone