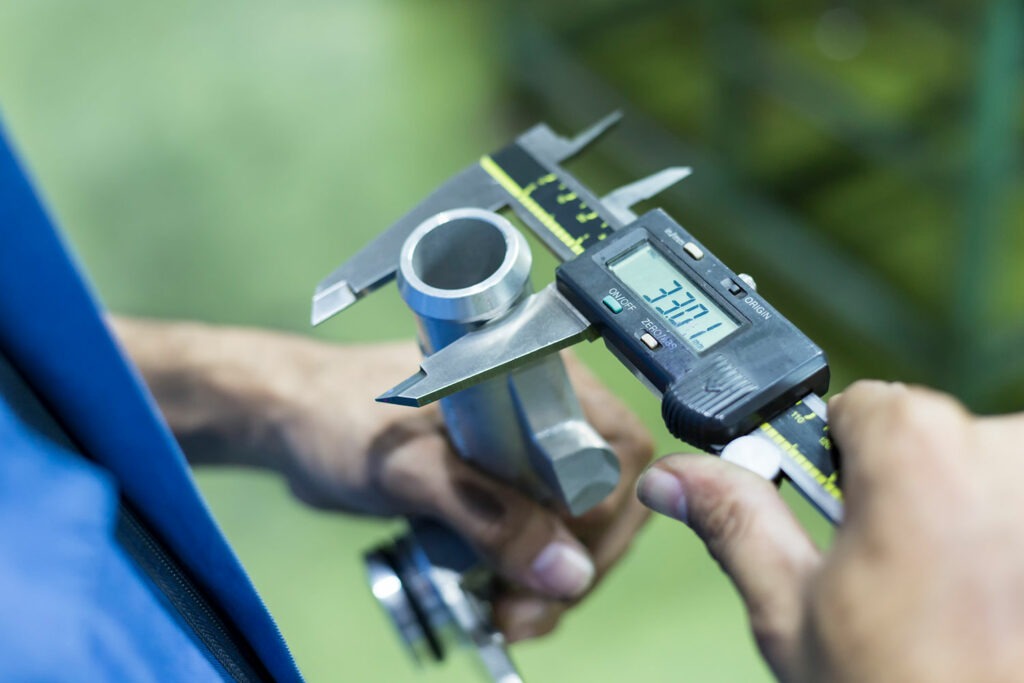
Interviewer: What are calibration, gauging, and adjusting?
Brij Suri: Calibration, gauging, and adjusting are all processes involved in ensuring that a measuring instrument or system is accurate and reliable. Calibration refers to the comparison of the readings of a measuring instrument with a standard reference to determine its accuracy. Gauging involves measuring the physical dimensions of an object using a calibrated tool such as a micrometer or caliper. Adjusting involves making small changes to an instrument or system to bring it into alignment with the standard reference.
Interviewer: What are the principles of calibration?
Brij Suri: The principles of calibration include accuracy, precision, traceability, and repeatability. Accuracy refers to the closeness of a measurement to the true value, while precision refers to the consistency of repeated measurements. Traceability means that the calibration is linked to a national or international standard, and repeatability refers to the ability to obtain consistent results when measuring the same object multiple times.
Interviewer: What is Pressure Calibration, Temperature Calibration, Flow Calibration, Pipette Calibration, Electrical calibration, Mechanical calibration? Please provide examples of equipment which need calibration for each of the categories above? Please explain those terms in detail and in the context of practical industry.
Brij Suri: Pressure calibration involves measuring and adjusting the accuracy of pressure measuring instruments such as gauges, transducers, and switches. Examples of equipment that require pressure calibration include pressure gauges, transmitters, and switches used in the oil and gas industry, HVAC systems, and pharmaceutical manufacturing.
Temperature calibration involves measuring and adjusting the accuracy of temperature measuring instruments such as thermocouples, RTDs, and infrared thermometers. Examples of equipment that require temperature calibration include ovens, refrigerators, and furnaces used in manufacturing, healthcare, and food processing.
Flow calibration involves measuring and adjusting the accuracy of flow measuring instruments such as flow meters, rotameters, and mass flow controllers. Examples of equipment that require flow calibration include water flow meters used in municipal water treatment plants, gas flow meters used in oil and gas pipelines, and mass flow controllers used in semiconductor manufacturing.
Pipette calibration involves measuring and adjusting the accuracy of pipettes and dispensers used in analytical and research laboratories. Examples of equipment that require pipette calibration include micropipettes used in molecular biology and drug discovery, and burettes used in analytical chemistry.
Electrical calibration involves measuring and adjusting the accuracy of electrical measuring instruments such as multimeters, oscilloscopes, and power meters. Examples of equipment that require electrical calibration include power analyzers used in the utility industry, test and measurement equipment used in electronics manufacturing, and signal generators used in telecommunications.
Mechanical calibration involves measuring and adjusting the accuracy of mechanical measuring instruments such as torque wrenches, force gauges, and dimensional measurement tools. Examples of equipment that require mechanical calibration include torque wrenches used in automotive and aerospace manufacturing, force gauges used in materials testing, and dimensional measurement tools used in quality control.
Interviewer: What is 5 point calibration? Off-site calibration and on-site calibration?
Brij Suri: 5 point calibration is a type of calibration that involves measuring an instrument at five different points across its range of operation to ensure accuracy and linearity. Off-site calibration involves sending an instrument to a calibration lab, while on-site calibration involves having a technician come to the facility to perform the calibration.
Interviewer: What is tolerance in calibration? Why is it important? What is accuracy ratio and why is that important? Please describe uncertainity analysis , why is it important and how is it done? What is calibration range, span and instrument range? How does one range an instrument? What is Zero and Span adjustments? What is field calibration?Bench tester?
- Brij: Tolerance in calibration refers to the acceptable deviation from a known standard or specification for a given measurement or instrument. It is important because it ensures that the equipment is operating within acceptable limits and produces reliable and accurate results.
- Accuracy ratio is the comparison between the measurement error and the total measurement range. It is important because it provides an indication of the overall accuracy of an instrument.
- Uncertainty analysis is the process of evaluating and quantifying the uncertainty associated with a measurement or calibration result. It is important because it helps to identify potential sources of error, estimate the overall uncertainty of the measurement, and improve the reliability and accuracy of the measurement system.
- Calibration range is the range of values over which the instrument is calibrated. Span is the difference between the upper and lower range values. Instrument range is the range of values that can be measured by the instrument.
- Ranging an instrument involves adjusting the zero and span values to ensure that the instrument is measuring within its range and producing accurate and reliable results.
- Zero and span adjustments are the process of adjusting the output signal of an instrument at the lower and upper range values to match the known standard or specification.
- Field calibration is the process of calibrating instruments at the actual site or location where they are used. Bench tester is a device or equipment used to test and calibrate instruments in a laboratory or workshop setting.
Interviewer: How can calibration contribute to sustainability?
Brij: That’s a very interesting question. Calibration can contribute to sustainability in several ways:
- Reduced waste: Accurate calibration ensures that measurements are correct and that equipment is functioning efficiently, which can reduce material waste and energy consumption.
- Energy conservation: Properly calibrated equipment can reduce energy usage, resulting in lower emissions and carbon footprints. For example, a properly calibrated HVAC system can reduce energy usage and result in lower greenhouse gas emissions.
- Compliance with regulations: Many industries are subject to regulations that require regular calibration of equipment to ensure environmental and worker safety. Compliance with these regulations can help reduce environmental damage and ensure that resources are used responsibly.
- Improved product quality: Calibration can help ensure that products meet quality standards, reducing waste and minimizing returns or recalls.
Overall, calibration helps to ensure that resources are used efficiently, waste is reduced, and compliance with regulations is maintained, all of which contribute to a more sustainable future.
Our qualified team of professionals would love to talk to you about questions or any requirements. Talk to our team now using the contact button for questions or needs.
Contact Us Via WhatsApp Contact Us Via Email Call Us Via Phone