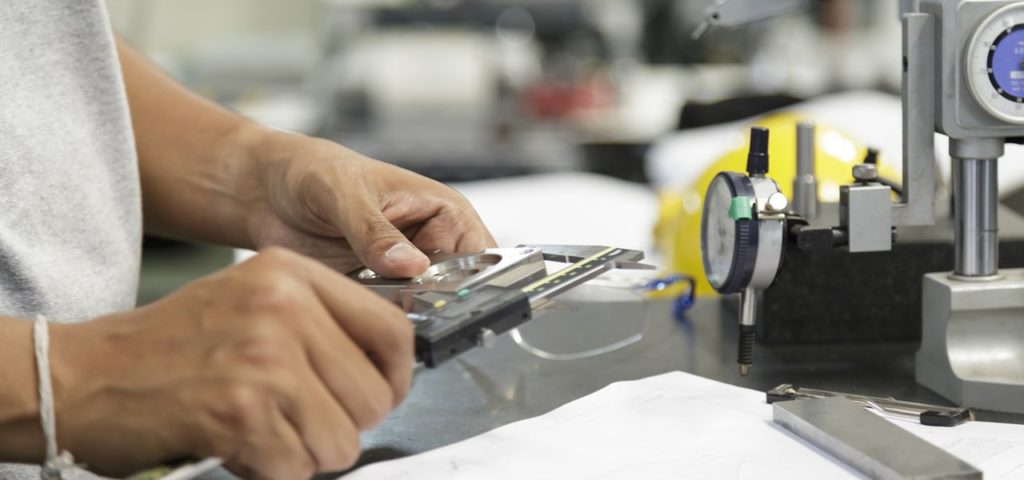
Interviewer: Can you discuss some common types of calibration and how they differ from each other?
Brij: Sure, there are various types of calibration, including dimensional calibration, electrical calibration, pressure calibration, temperature calibration, and flow calibration. Each type of calibration requires different methods and equipment. For example, dimensional calibration involves the comparison of the dimensions of a test object to a standard, whereas electrical calibration involves the comparison of an instrument’s electrical output to a standard. Pressure calibration involves the comparison of a pressure gauge to a standard, while temperature calibration involves the comparison of a temperature sensor to a standard. Flow calibration involves the comparison of a flow meter to a standard. Each type of calibration requires careful attention to detail and the use of accurate reference standards.
Performing Calibration
Interviewer: Can you explain how instrument calibration is performed?
Brij: Sure, instrument calibration is typically performed by comparing the readings of the instrument being calibrated to a traceable reference standard. The reference standard can be a calibrated instrument, a national standard, or an international standard. The process usually involves adjusting the instrument to bring it into alignment with the reference standard, with the aim of reducing the difference between the instrument’s readings and the true value. The calibration process can be performed in-house, or by a third-party calibration service provider.
Interviewer: Can you explain how validation and mapping fit into the process of instrument calibration, and which industries need to do this?
Brij: Sure, validation and mapping are important processes that are closely related to instrument calibration. Validation is the process of verifying that an instrument or system meets its intended requirements and specifications. It is typically performed during the design and development of a new product or process, and it involves testing and analyzing the performance of the instrument or system. Validation ensures that the instrument or system performs as expected and meets the required standards.
On the other hand, mapping is the process of measuring and recording temperature, humidity, or other environmental factors at various points within a space or chamber. Mapping is typically performed in industries that require precise control of environmental conditions, such as pharmaceuticals, biotechnology, and food and beverage production. The data collected during mapping is used to verify the uniformity and stability of the environment, and it can be used to identify areas where calibration may be required.
Industries that require precise control of environmental conditions, or that rely heavily on measuring instruments, are the ones that typically require validation and mapping. This includes industries such as pharmaceuticals, biotechnology, medical devices, aerospace, automotive, and food and beverage production. These industries have strict quality standards and regulations that require precise measurement and control of environmental factors, and therefore, validation and mapping are essential to ensure compliance and safety.
Talk to our team now using the contact button for questions or needs.
Our qualified team of professionals would love to talk to you about questions or any requirements. Talk to our team now using the contact button for questions or needs.
Contact Us Via WhatsApp Contact Us Via Email Call Us Via Phone