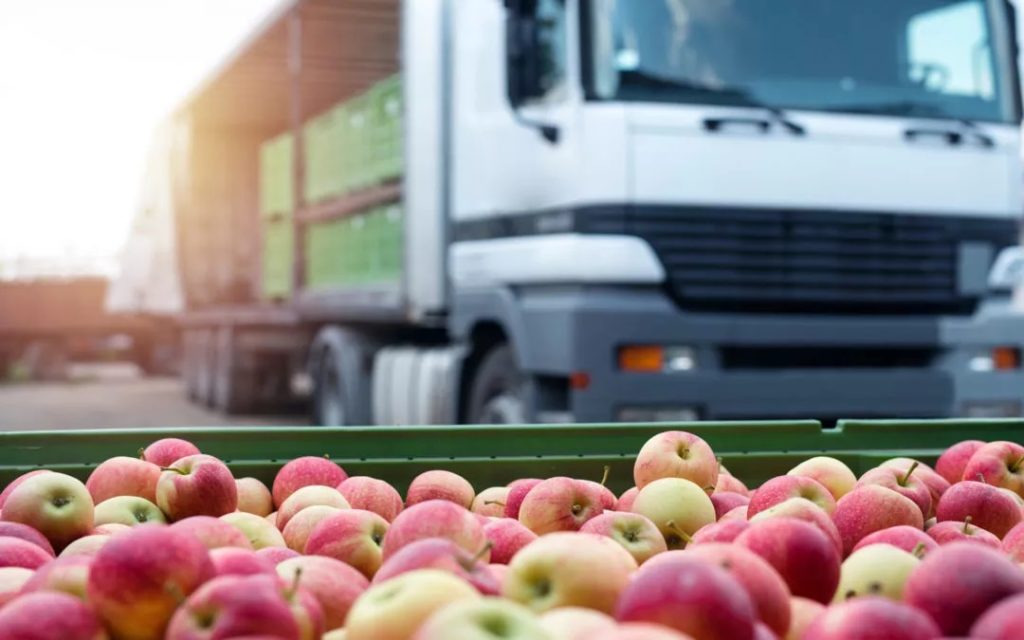
It is well-established that cold chain management is a must to ensure that food and pharmaceutical products can be delivered safely within the supply chain. But there are several sub-components that make up the larger process of cold chain management. Let’s look at some of the sub-processes that must be executed properly to ensure effective cold chain management.
Data loggers
First, we have data loggers. These are an important tool in cold chain management as they help in monitoring and recording temperature and other environmental parameters during storage and transportation of temperature-sensitive products. They provide valuable data that can be used for analysis, decision-making, and quality control. The traits of a good data logger include accuracy, reliability, and compatibility with the specific cold chain requirements. We offer best-in-industry, easy to use and efficient data loggers to ensure that your products reach their destination safely.
Mapping
Next, we have mapping which refers to the process of creating a visual representation of temperature and other environmental conditions throughout the cold chain. This is done by
placing data loggers at strategic points along the supply chain and analysing the resulting data to identify areas that need improvement. This exercise helps to identify areas of temperature variation, potential risks, and opportunities for improvement. A good mapping exercise should include a clearly defined scope, proper placement of data loggers, appropriate data analysis methods, and collation of comprehensive reports. Our mapping experts check all parameters thoroughly and offer a detailed analysis in their reports.
Validation
Validation is what comes next. This is the process of verifying that the cold chain system meets the desired specifications and is performing as intended. It involves testing the temperature control systems and procedures under different conditions to ensure that it can maintain the required temperature range for the specific product. Validation helps to ensure product quality, reduce the risk of product spoilage or loss, and comply with regulatory requirements. This can be done through simulated tests or real-world tests that our world-class experts are adept in executing.
Risk assessment
At the final stage, comes risk assessment. This is the process of identifying and analyzing potential risks in the cold chain system and implementing measures to mitigate them. It involves assessing the likelihood and severity of risks associated with temperature excursions, equipment failure, human error, and other factors. Risk assessment helps to ensure product safety, reduce the risk of product loss, and comply with regulatory requirements. Risks may include temperature fluctuations, power outages, or transportation delays, among others. Tools and technologies such as predictive analytics and real-time monitoring systems can help to mitigate these risks.
Thus, effective cold chain management has multiple elements and they must all come together successfully to eliminate any product loss or spoilage.
Our qualified team of professionals would love to talk to you about questions or any requirements. Talk to our team now using the contact button for questions or needs.
Contact Us Via WhatsApp Contact Us Via Email Call Us Via Phone